こんにちは、ネイトです。
今回は、
「旋盤で失敗して対策を立てる方法!」
について述べていこうと思います。
この記事を書こうと思ったのが、
ネット上や書籍に、
汎用旋盤の加工ミスなどの
失敗を減らすための情報が全くなく、
旋盤で失した時の対策の立て方について、
問い合わせを多くいただくようになったからです。
僕自身、汎用旋盤を使い始めて間もない頃、
月に10件ほど失敗して、
1年ほどで100万円以上の損害を出し、
社長や上司に吐くまでボロカスに怒られて、
辛い日々を過ごしてきました。
なんとか失敗を減らそうと思い、
本で失敗しない方法を学ぼうとしても、
旋盤の不良品対策が書かれた書籍はなく、
自分で勉強ができなかったんですね。
「なんで旋盤の各部の名称や使い方の本しかないんだ?」
と心の中で何度も思いましたね。
今でこそ、たくさん経験を積んできて、
「どうしたら失敗を減らせるか」
「この失敗の場合はどう対策したらいいか」
というのが分かるようになりましが、
その道のりは決して
平坦なものではなかったです。
これだけネットが発達した今でも、
旋盤で失敗した時の対策法は
ネット上に見当たらなく、
「どうしたら旋盤で失敗を減らすことができるのか分からない」
という話も多く聞きます。
旋盤で失敗した時に対策を立てないと、
同じ失敗を繰り返してしまい、
上司や先輩にボロカスに怒られてしまい、
嫌な思いをしてストレスを溜めながら
仕事をするようになります。
さらに、失敗が多いと給料やボーナスの査定に
悪影響を与えてしまい、下がってしまう可能性が高くなり、
仕事を続けるモチベーションを保つのが難しくなります。
僕が過去にいた会社で失敗が多い人が、
月1万円減給された方もいて、
「きちんと対策立てたら失敗しなくなるのにな~」
と遠目に眺めていました。
せっかく旋盤を覚えようと一生懸命頑張っているのに、
失敗して上司や先輩に怒られたり、
給料やボーナスが下がると、
頑張って覚えようという気持ちがなくなりますよね。
そこで、昔の僕と同じように
失敗が多くて上司や先輩に怒られて悩んでいる方のために、
旋盤で失敗を減らすための対策の立て方を
紹介しようと思います。
目次
旋盤で失敗した内容を分析して2つの要因に分ける
旋盤で失敗した場合、
内容に合わせた対策を立てる必要がありますが、
まず最初にやるべきことは、
対策を立てやすいようにするために、
失敗した内容を分析して、
■加工中の失敗
■加工中以外の失敗
の2つに分けることです。
そして、それぞれの内容に対して
最適な対策をすることで、
誰でも失敗は大幅に減らせます。
それぞれの失敗内容を具体的にいいますと、
加工中の失敗は、基本的に加工中に起きた失敗。
ドリルが折れた、
タップが折れた、
製品が飛んで傷が入った、
寸法公差が外れた、
切削油を使わなかったので、仕上げ面が汚くなった、
など、上記のような加工中に起きた内容が該当します。
次に加工中以外の失敗は、
■図面の寸法を見間違えて加工した、
■計算間違いをして、その間違えた寸法で加工した、
■マイクロメーターを0,5mm読み間違えて失敗した、
といった感じの
主にケアレスミスが原因の失敗になります。
旋盤で失敗してしまった場合、
内容を分析して最初にこの2つに分けて、
それぞれの内容に合わせた対策を立てると、
効率よく失敗を減らすことができるのです。
逆に失敗しても対策を立てずに放置した場合、
何度も何度も同じ失敗を繰り返し、
上司や先輩にボロカスに怒られて、
給料やボーナスも下がる可能性もあります。
そうならないようにするためにも、
失敗したら必ず原因を見つけて、
原因に合わせた対策をして、
同じ失敗を繰り返さないようにすることが
非常に大切になってきます。
加工中に起きた失敗の対策の立て方
加工中に起きた失敗の対策は、
加工中以外に起きた失敗と比べて、
それほど難しくなく、
個別の内容に合わせて
対策するだけで大丈夫です。
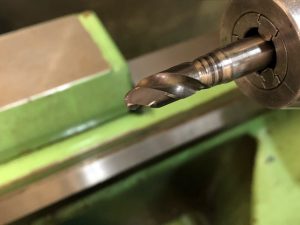
ドリルが折れて製品から抜けなくなった。
という内容の失敗なら、
ドリルが折れた原因を見つけて、
対策するだけです。
ドリルが折れた原因が
切粉を抜かずにドリルを一気に入れてしまい、
切粉が詰まってドリルが折れた。
と言うのであれば、
こまめにドリルを抜いて、切粉を除けてやる。
という対策をしてやれば、
同じ失敗はしなくなります。
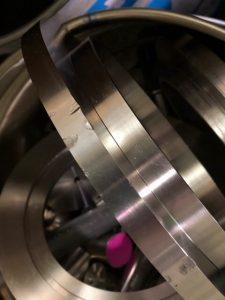
切削時に製品が動いて傷が入った。
という内容なら、
製品が動いてしまった原因を見つけて
きちんと対策をするだけです。
製品を軽い力でしか掴んでないのに、
主軸を最高回転で回転させたから、
遠心力でチャックが開いて製品が動いた。
というのが原因なら、
回転数を落として加工するか、
もう少しチャックを強く締めて加工すれば
問題ありません。
切削抵抗が強くて、
製品が動いてしまった場合。
切り込みを少なくするか、
切削抵抗の少ないチップに変える。
もしくは回転センターで抑える。
といった感じで、
失敗の内容に対して原因を見つけて、
個別に対策を立ててやるだけなのです。
このような感じで
加工中の失敗は個別の内容に対して、
対策を立ててやることで、
自然と減っていきます。
加工中以外に起きたケアレスミスが原因の対策の立て方
加工中の失敗の対策よりも、
■図面を見間違えて違う寸法で加工してしまった、
■計算間違いをして、違う寸法で加工してしまった、
■マイクロメーターを0,5mm読み間違えて削りすぎてしまった、
という内容の加工中以外に起きた、
ケアレスミスが原因の失敗の対策の方が
かなり重要だったりします。
というのも加工中の失敗は、
経験を積み重ねていくたびに、
自然と体が覚えていき、
減っていく傾向にあります。
しかし加工中以外の失敗、
いわゆるケアレスミスが原因の失敗は、
きちんとした対策を立てないと
どれだけ経験を積んでも
同じケアレスミスが原因の失敗を
何度も繰り返してしまいます。
旋盤歴10年以上あって、
どれだけ難しい製品が加工できるとしても、
ケアレスミスが出なくなる対策をしてなければ、
勿体ない失敗をたくさんしてしまうのです。
今まで色々な職人さんを見てきましたが、
そういう勿体ない失敗をする方を
たくさん見てきました。
そこでケアレスミスが原因の
失敗の対策法を紹介するのですが、
この失敗の対策法は、
ケアレスミスが出ないようにする
作業手順書を作ることです。
ケアレスミスが出ない手順書って
どのような作業手順書かといいますと、
図面を見てから加工に入るまでに、
この手順で図面チェック、段取りをしたら、
ケアレスミスが原因の失敗が出なくなる、
という作業手順書です。
いわゆる加工前の作業手順書ってやつですね。
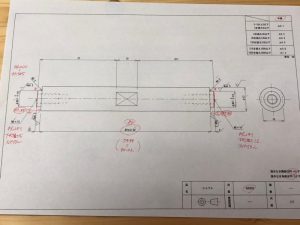
例えば図面を見てから
加工する寸法をチェックした時に、
計算を間違えて、違う寸法を図面に記入したら、
その間違えた寸法で加工してしまいますよね。
そして計算間違いに気が付かないまま、
加工して失敗してしまい、
それまでの加工時間が無駄になってしまいます。
そのような勿体ない失敗をなくすために、
加工する前に図面を見てから、
図面の中でチェックする項目は何か?
どの順番でチェックしたらいいのか?
どの工具で加工したらいいのか?
といった内容を手順としてまとめ、
作業手順書通りに図面チェック、段取りをしたら、
図面の見間違えや計算間違いによる
ケアレスミスが原因の失敗が出なくなる
作業手順書を作ることが大切なのです。
作業手順書の効果は、
僕が一番よく知っています。
僕自身、見習いだった頃に失敗が多く、
社長や上司に毎日ボロカスに怒られ、
クビ寸前まで追い詰められました。
(僕の旋盤で失敗が多かった頃のストーリーはこちら)
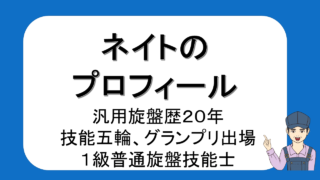
しかし、なんとか仕事ができるようになりたいと思い、
師匠に手伝ってもらいながら、
失敗の内容を分析して、
対策を立てるようにしました。
自分の失敗の内容を分析したところ、
図面の見間違えや、計算間違いなどの
ケアレスミスが原因の失敗が
70%以上締めるという、
非常に勿体ない失敗ばかりしていました。
そこで、ケアレスミスが出なくなるための
作業手順書を作って実践したところ、
毎日のように失敗していたのが、
1週間0件から始まり、
2週間、3週間、1か月と続いて、
最終的に1年間失敗0件を達成することができたのです。
そして失敗が減ることで、再製作の時間などの無駄も減り、
売り上げが作業手順書を作る前の3倍にアップしました。
その結果、今までボロカスに怒られてきた社長や上司からも
仕事に対する信頼を得ることができ、
給料月3万アップ、ボーナス100万円もらうことが
できました。
たかが加工する前に図面チェックをする
手順書を作るだけかもしれませんが、
作った僕もめっちゃびっくりするくらい、
想像以上に絶大な効果がありました。
そのくらいケアレスミスが原因の失敗対策として、
作業手順書を作ることは
重要になってきます。
この僕が作った作業手順書ですが、
昔の僕のように、旋盤での失敗で悩んでいる方から
「教えてもらえませんか?」
と多数お問合せをいただいております。
お問合せをいただくたびに、
正直公開するか非常に迷いました。
と言うのも作業手順書は
僕が20年近くかけて学んできた内容の中でも
選りすぐったものを凝縮させており、
公開することでライバルを一気に
増やしてしまう可能性があるのです。
だから、公開するか本当に悩みました。
しかしこの記事を読まれる方は、
昔の僕と同じように、
旋盤での失敗に悩んでおられると思います。
僕も旋盤で失敗が多くて悩んでいましたので、
そういう方の気持ちは痛いほどよく分かります。
そこで、そのような方の力になりたいと思い、
僕が作って販売している作業手順書の一部を
無料でダウンロードできるようにしております。
無料体験版とはいえ、
皆様のお役に立てればと思い、
作業手順書の中でも重要な部分を
無料体験版として公開しています。
是非、作業手順書を活用して、
失敗を減らすために役立てていただけたらと
思います。
失敗を経験すると財産になる・・・・だけど対策は必要。
僕の意見として、
汎用旋盤での失敗は、
たくさん経験しておくべき
と思っています。
(同じ内容の失敗は除く)
旋盤を使って失敗を経験することで、
「こうなったら失敗する」
ということを学ぶことができ、
その失敗の原因に対して対策を立てることで、
自分の財産となるからです。
そして新規の仕事をやる時など、
今まで失敗した経験を生かして、
失敗しないように予測を立てて
加工する事ができるようになります。
すると、あまり失敗してこなかった人と比べて、
「こうなったら失敗する」という経験があるので、
新規の仕事でも失敗することが少なくなり、
上司や客先からも信頼して
仕事をもらえるようになります。
さらに、自分が初めて加工する仕事で
失敗しにくくなるだけではなく、
他の人に教える時にも、
役に立つようになるのです。
自分が失敗の経験して原因を見つけて、
対策を立てることをやってきているので、
教えている人が失敗した場合でも、
素早く失敗した原因を見つけて、
対策を立ててあげることができます。
そして後輩もどんどん育っていき、
自分が今までやっていた仕事を
任せられるようになります。
すると自分は今まで以上、
付加価値の高い仕事をできるようになり、
売上がアップして、給料、ボーナスも上がる
可能性があるのです。
だから、僕は旋盤での失敗を
たくさん経験して対策することで、
自分の財産が増えると
考えています。
しかし、
「たくさん失敗を経験した方がいい」と言っても、
失敗したらきちんと対策を立てて、
同じ失敗を繰り返さないようにしないといけません。
そうしないと、失敗が自分の財産にならずに、
ただのゴミと化してしまうからです。
過去の僕は、
そのことに気が付いておらず、
失敗しても原因を見つけて
対策を立ててきませんでした。
その結果、
何度も何度も図面の見間違えなどの
ケアレスミスが原因失敗を繰り返してしまい、
社長や上司に毎日のように
ボロカスに怒られ続けました。
精神的にも肉体的にも辛い日々で、
今思い出すだけでも鳥肌が立ってしまうくらい、
辛い日々でした。
しかしきちんと失敗した原因を見つけて
作業手順書を作ることで、
失敗を減らすことに成功。
今までボロカスに怒られてきた
社長や上司からも褒められるようになり、
給料、ボーナスも大幅にアップして、
それまでの辛い日々とは180度逆になったのです。
そしてこのたくさん失敗して
学んできたことを糧にして、
今までよりも難しくて高付加価値な仕事も
加工できるようになり、
飛躍的に成長することができました。
しかし今まで色々な会社の方を
見る機会がありましたが、
きちんとした失敗の対策をやっている会社は、
マニュアルがある一部の会社を除き、
ほとんどありませんでした。
ネット上にも旋盤で失敗した時の
対策の情報は皆無に等しく、
自分で調べて勉強しようにも、
やりようがないのが現状です。
その結果、
失敗して対策を立てたくても立てれずに、
上司や先輩にボロカスに怒られて、
辛い思いをしている方も
たくさん見てきました。
せっかく旋盤を覚えようと頑張っているのに、
失敗の原因の見つけ方や対策の立て方が、
わからないので改善できないのは、
ほんとうに勿体ないんですよね。
そのような方の力になれればと思い、
作業手順書を一部無料で公開しておりますので、
是非、活用して失敗した経験を財産にして
いただけたらと思います。